衝撃ロガーを用いた落下高さ解析の検討
包装貨物は、その荷役作業時に落下衝撃に遭遇し、中身の製品が損傷する場合があります。
このような物流過程での製品破損を防ぐためのツールとして、荷役作業時の落下衝撃の発生程度を抑制するShockWathがあります(ShockWatch検証実験結果はこちら)
その他の対応としては、荷役中に落下が生じても、製品を保護できる緩衝性能を有した包装設計を施すことが挙げられます。
ただし、緩衝材料を多量に使用してしまうと、過剰包装となり、無駄なコストが発生してしまいます。そこで適正包装設計(最小限の緩衝材コストで製品を十分に保護できる包装仕様)が求められます。
適正包装設計を実現するためには、①荷役中の落下衝撃から包装貨物落下試験高さへの換算、②製品の衝撃強度を把握する必要があります。
これまで、①の落下衝撃データの記録と解析は、比較的高機能な輸送環境記録計が用いられていますが、ここでは、より簡便な記録と解析を行うことを目的とし、衝撃ロガーを利用した事例を紹介します。
輸送データ測定条件
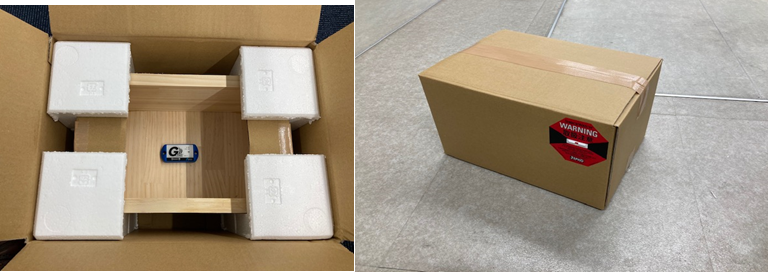
データ記録用包装箱:木箱ケース約2㎏の中央に衝撃ロガーShockView(加速度トリガ10G設定)をネジ固定
輸送区間:神戸⇔つくば
輸送回数:3往復
実データからの落下高さ変換
衝撃ロガーでは、発生した衝撃加速度の最大値(3方向)が記録されますが、これを落下高さに換算する必要があります。このためには、事前試験として、落下試験による衝撃データ取得が必要です。具体的には、包装貨物落下試験機にて、実際に輸送させる包装箱を低い落下高さから、徐々に落下高さを上げていき、それぞれの高さで貨物内に発生する衝撃値を記録することで、落下高さ-最大加速度グラフを算出します。
次に、このグラフの近似曲線を算出します。これにより、離散データを連続データとして取り扱うことができます。図1はその一例です。
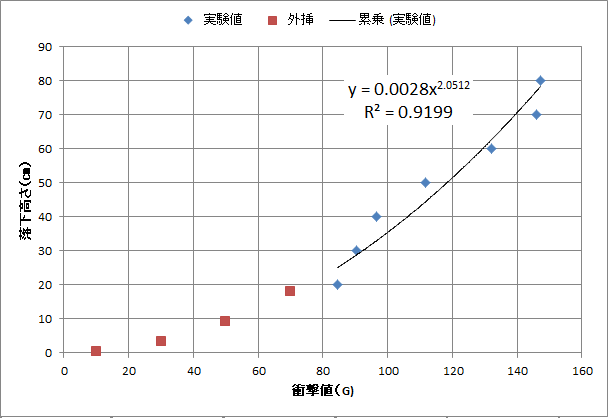
ここで落下高さ-最大加速度グラフの近似曲線に対し、実輸送で記録した衝撃値を代入することで、想定落下高さが得られます。
図2は実際に記録した衝撃データを、図1から落下高さに換算したときの度数分布(3往復累計)と、その累積分布を示しています。ここで、累積分布を分布関数に近似することで、落下高さを連続データとして取り扱うことができます。図3はその一例として、ワイブル分布関数を適用した例を示しています。
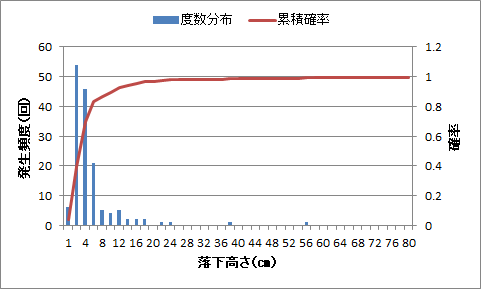
その後、許容される累積発生確率を設定すれば、包装貨物落下試験の試験高さを設定することができます。たとえば、全輸送のうち99%は安全に運びたい(試験落下高さに遭遇させない)ことを想定した場合、必要な落下高さは図2の累積分布から35㎝となります。
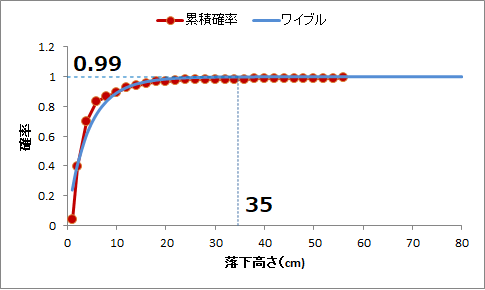
このような落下高さ設定方法は、各種ある手法のうちの一つであり、必ずしも本手法が絶対ではないことを念頭に置いた上で、一つの参考例としてご参照いただければ幸いです。
衝撃ロガーShockViewについて
衝撃ロガーShockViewはこちら(Amazon)からご購入ができます。